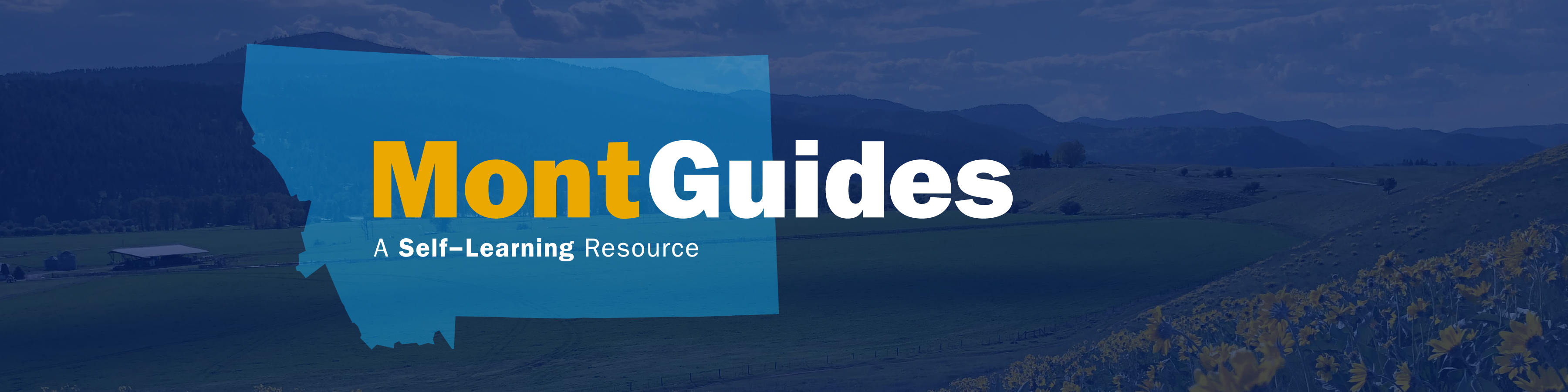
Maintenance, Cleaning and Storage of Ground Sprayers
Proper storage and cleaning techniques can add years to the life of spraying equipment. This fact sheet offers tips for preparing pesticide spraying equipment to be stored for the winter, including a list of which cleaning agents are most effective for various pesticides.
Last Updated: 03/23by Reeves Petroff, MSU Extension Pesticide Education Specialist, and Dr. Greg Johnson, MSU Entomology Department Head Revised by Dr. Cecil Tharp, MSU Extension Pesticide Education Specialist, and Amy Bowser, MSU Extension Pesticide Education Technician
THE SPRAYING SEASON IN MONTANA OFFERS
such a limited window of opportunity you can’t afford to lose extra days getting spray equipment into shape. Proper maintenance and storage techniques not only streamline next year’s pre-season preparations, but also enhance sprayer performance while adding years to its productive life. By cleaning the pesticide spray tank an applicator can minimize future crop injury from unintended residues remaining in spray tank.
Long-term exposure to many pesticides can corrode and deteriorate sprayer parts, paint and electrical connections. The residue from these products may be harmful to anyone working on or around the machine. Also, trace amounts of pesticides lodged in sprayer parts may damage crops if carried over to the next spraying season.
Personal safety and that of your family, employees and storing crops make it important to thoroughly clean and decontaminate a sprayer during the season, between crops and before storing it for the winter.
A complete maintenance and storage process consists of six steps:
- Read
- Select location and pre-rinse
- Dispose of rinsate
- Clean
- Inspect
- Store
1. Read
Before cleaning your sprayer, be sure to review the labels of the pesticides applied. The label will:
- Tell how to properly dispose of residual product.
- Provide any special cleaning instructions.
- Recommend cleaning products.
- Outline the personal protective equipment (PPE) needed to safely clean a sprayer.
2. Selecting Location and Pre-Rinse
Select a location where the rinse material will not contaminate water supplies, streams, crops or other plants and where large puddles won’t accumulate, creating a hazard to humans, animals and the environment. Alternatively, the rinsate may be disposed in an area impervious to water with a wash rack or cement apron with a sump to catch contaminated wash water and pesticides.
The goal of pre-rinsing is to remove pesticide product and residue still in or on the sprayer. Pre-rinsing spray equipment involves circulating water through the whole system and then applying it to a site listed on the label of the pesticides used. Several rinses using a small volume (up to 10 percent of the spray tank capacity) are better than merely filling the spray tank once with clean water.
Make sure to dispose of rinsates from the spray tank in a manner consistent with the pesticide label. Don’t just open the valves and let it pour on the ground.
The outside of the sprayer should also be washed. For this purpose, applicators are encouraged to have a source of water on the sprayer in order to rinse down the sprayer in the field on a regular basis. Again, when rinsing the sprayer, do not create standing puddles that might be accessible to humans, pets, livestock or wildlife.
3. Disposing of Rinsate
To dispose of pesticide rinsate in accordance with label directions, apply the rinsate to a site where the products are to be used originally. In other words, the site must be listed on the label. Repeat the disposal process after cleaning and rinsing the sprayer. Rinsate containing cleaning products such as bleach, fuel oil, or kerosene should not be sprayed on agricultural plants. If using these cleaning products an applicator should consider using a pesticide handling facility when disposing of rinsate.
4. Clean
After your sprayer has been pre-rinsed, it’s time to clean or decontaminate it.
Be sure to decontaminate both the interior and exterior of the machine, running liquid through the boom structure and out the nozzles. It is unnecessary to fill the sprayer. Use only enough cleaning solution to completely fill the lines and provide enough agitation. You may need to scrub or power wash the inside of the tank. Wear personal protective equipment (PPE).
Select cleaning agents and follow procedures outlined on the pesticide product label if provided. If not listed on the label, applicators may select cleaning agents and follow procedures outlined in Table 1. Cleaning agents should penetrate and dissolve pesticide residues and allow them to be removed when the rinsate is removed from the sprayer. Commercial tank cleaning agents and detergents help remove both water- and oil-soluble herbicides and are recommended on many pesticide labels.
Some commercial tank cleaning agents and ammonia solutions raise the pH of the rinsate solution, making some products such as sulfonylurea (SU) herbicides and insecticides more water soluble and thus easier to remove from internal sprayer parts.
Chlorine bleach solutions hasten the breakdown of SU’s and some other herbicides into inactive compounds. However, chlorine is less effective at dissolving and removing SU herbicide residues from spray tanks than ammonia solutions. Never add chlorine bleach to ammonia or liquid fertilizers containing ammonia, because the two materials react to form toxic chlorine gas.
Fuel oil or kerosene is effective for removing oil-soluble herbicides such as esters and emulsifiable concentrates. The fuel oil or kerosene should be followed by a detergent rinse to remove the oily residue. Also run cleaning solution through the sprayer, including the agitation system and the return lines. Then rinse the system with clean water. Finally, remove nozzles and screens prior to soaking in cleaning detergent for 24 hours, then rinse prior to storage.
5. Inspect
After the final rinse, inspect the sprayer and make the necessary repairs and modifications. Even though the sprayer has been “cleaned,” always wear personal protective equipment; some residue may remain on and in the sprayer.
Here is a checklist of what to look for both during and after cleaning:
- Mismatched and worn nozzles
- Damaged nozzle screens
- Damaged strainer screens
- Cracks, leaks and overall performance in the pump.
- Hose condition, especially brittleness or cracks
- Valve condition, identifying any possible leaks or areas where seals may have loosened
- Boom structure, identifying any cracks that must be fixed
Modifications
Some modifications to sprayer equipment can make cleaning the equipment easier:
- Shut-off valves on either side of the pump to facilitate pump removal and repair
- Shut-off valves at the boom
- Shut-off valves at the tank
- Additional pressure gauges
- Installing flowmeters
- Installing tank level indicators
- By-pass and agitation lines
- Engine-kill switches
- Additional lines to aid in cleaning (i.e. broadjets for spraying out rinsate as opposed to using booms)
6. Store
Now that the sprayer has been thoroughly cleaned, consider removing parts easily damaged during storage.
- Remove strainers (filters) and wash them by hand with soapy water (remember to wear chemical-resistant gloves), rinse them and either store them or place them back in the sprayer.
- Pay special attention to nozzles, nozzle bodies and check valves. Chemical residue can build up in these areas and harden over winter, dramatically reducing the sprayer’s performance next season.
- Remove nozzle tips, screens, check valves, caps and nozzle bodies from the nozzle body assemblies. Correctly plug the assemblies.
- Clean and rinse out the nozzle tips, nozzle bodies and check valves. Store in a marked container. Store check valves at room temperature over the winter to avoid damage that can be caused by freezing temperatures.
- Remove all pressure gauges and cap the openings on the sprayer. Store the gauges where they are not subjected to freezing or damage.
Finally, circulate antifreeze through the sprayer and all plumbing, including booms, valves, manifolds, flowmeters and agitation/return lines. Allow the antifreeze to circulate through the boom’s hoses. This will coat the hose linings to prevent drying out and cracking. Capping all boom nozzles will help retain the antifreeze in the system, but you may need to open one or two nozzles to allow the antifreeze to circulate through the boom. Cap those nozzles when antifreeze has completely filled the system.
The goal for the storage phase is for the antifreeze to push out residual water that may be in the system and to coat all of the sprayer’s components. Allow the antifreeze to sit in the pump and valves to avoid rusting and damage that can be caused by moist air being trapped in the system. Since some applicators remove the pump prior to storage, the installation of shut-off valves on either side of the pump can facilitate this process.
Anti-freeze for recreational vehicles (RVs) is commonly used for storage of agricultural sprayers. Unlike automotive antifreeze, it is less toxic to animals. While many RV antifreeze products will gel in extremely cold conditions, they should not freeze. Regardless, always read the antifreeze label to make sure it will perform under winter conditions.
Now that the sprayer has been cleaned, decontaminated and winterized, it’s ready to be stored. Indoor storage away from the elements, is preferable. But any indoor site should be far away from both liquid and dry fertilizers. The dust and residue from these products can corrode both paint and hardware on the sprayer.
If you have a spray monitor, remove the display pad from the cab and store it in a warm, dry place.
Don’t forget foam markers and flowmeters
When cleaning and winterizing a sprayer, don’t overlook the foam marker system and any flowmeters. Start with the marker system. Simply disassemble the foam generators, then clean residue from the mixing filters and screens using clean water and the appropriate cleaning solution. Consult the manufacturer’s instructions of the foam marker to determine if specialized cleaning solutions are needed.
If you don’t clean out the spongy mixing filter, the residual foaming agent may harden, making it nearly impossible to clean later.
To clean the flowmeter, follow procedures outlined in the manufacturer’s instructions. Otherwise, use the following procedure where applicable. Be sure to determine if any warranties are affected.
- Disconnect the wiring harness from the electrical connector on the sensor.
- Unscrew the flowmeter insert and remove.
- Clean insert with clean, soapy water. Make sure the turbine turns easily. If it doesn’t, clean again.
- Reinstall insert in flowmeter.
- Attach electrical connector to sensor.
TABLE 1. Cleaning Solutions for Pesticides*
Pesticide Used |
Step 1 (25 Gallons Cleaning Solution) |
Step 2 |
Step 3 |
Hormone Herbicides(2,4-D salt, amine, brush killers, MCPA, dicamba) |
1 qt. household ammonia | Agitate solution for 15 minutes. | Let stand overnight. Flush with clean water. |
– OR – | |||
1 lb. washing soda (sal soda) | Agitate solution for 15 minutes. | Let stand for 2 hours. Flush with clean water. | |
– OR – | |||
2 lb. trisodium phosphate | Agitate solution for 15 minutes. | Let stand for 2 hours. Flush with clean water. | |
– OR – | |||
½ lb. fine activated charcoal +½ cup detergent | Agitate sprayer for 2 minutes. | Let stand for 10 min. Flush with clean water. | |
Hormone herbicides, ester form (2,4-D, brush killers, MCPA) | 1 lb. washing soda (sal soda) + 1 gal kerosene + ¼ lb detergent | Rinse inside of tank and flush small amount through system. | Let stand for 2 hours. Flush and rinse. |
Amino Acid Inhibitors(SU’s including primisulfuron, prosulfuron, and halosulfuron) | 2% household ammonia then circulate for 15 minutes and flush. | 1% household ammonia, circulate for 15 mins then flush. | Rinse tank for minimum of 5 minutes using clean water. |
Organophosphate or carbamate insecticides | 1 qt. household ammonia +¼ lb detergent | Flush a small amount through system. | Rinse with clean water. |
Other herbicides and insecticides | ¼ lb detergent | Flush a small amount through system. | Rinse with clean water. |
* Applicators should always read and follow any pesticide product label cleaning instructions.
Maintaining sprayer equipment
Maintenance of pesticide application equipment includes regular inspection of the spray tank, pump, hoses, line strainers, pressure gauge, fittings, nozzle tips and strainers. Check the sprayer prior to and following extended storage, and before each use. Remember to always wear personal protective equipment when handling spray equipment.
Spray tanks
Spray tanks are made of stainless steel, galvanized steel, fiberglass or plastic, including polyethylene or polypropylene. These materials are fairly non-absorptive, so no pesticide residues should be left in them after being cleaned. However, fiberglass tank linings, if scratched, will absorb pesticides. Cracks and chips in the epoxy coating of galvanized tanks must be repaired with epoxy material; otherwise, the exposed metal may corrode. Periodically check tanks for cracks, rust or corrosion that will weaken the tank and eventually develop into a leak. Make sure the spray tank is securely fastened to the sprayer.
Pump and Pump Seals
The pump and all its components must be in good working condition. Pump seals, ‘O’ rings or cup washers of leather or synthetic material may dry out and shrink if the sprayer has not been used for an extended period or stored improperly. The solvents in some pesticide formulations can damage pump seals, resulting in leaks around the pump or inefficient pumping.
Hoses
Replace cracked or leaking hoses. Remember, hoses used to apply pesticides can never be completely decontaminated. There will always be some pesticide residue left in them. Hoses that are replaced must be properly disposed of and not reused for any other purpose.
Line Strainers and Screens
Always use strainers and screens when the equipment is in operation. These filter out debris and foreign particles that can plug nozzles and reduce sprayer performance.
Pressure Gauges
Fluid pressure in the spray system is monitored by a pressure gauge, which measures spray pressure through the nozzles when located between the pressure regulator and spray nozzles. Consequently, a change in pressure can mean a potential malfunction. Make sure pressure gauges are in working condition and properly calibrated.
Fittings and Clamps
Loose or cracked fittings are frequently a source of leaks. Make sure fittings and clamps are snug prior to putting the system under pressure and pumping liquid. Once the system is under pressure, check for leaks.
Nozzle Tips and Strainers
Nozzles may be worn or damaged, preventing uniform spray coverage. All nozzles need to be applying the same amount of liquid within an error range, usually 10 percent on either side of the average. Clean and/or replace any nozzles outside of the error range. Replace them when wear causes flow to exceed that of a new tip by five to 10 percent.
For example, suppose the nozzle tip manufacturer states that nozzle tips should provide 50 ounces of flow per minute at 30 pounds per square inch (psi). Using an error range of 10 percent (0.10), simply multiply 50 x 0.10 and add to 50 to find the upper limit (50 ounces x 0.10 = 5 ounces; 5 ounces + 50 ounces = 55 ounces).
Subtract 5 from 50 to find the lower limit (50 ounces - 5 ounces = 45 ounces). Any flow volume at 30 psi between 45 and 55 ounces of flow per minute is acceptable. Anything above 55 or below 45 ounces per minute is not acceptable and nozzle tips should be cleaned or changed.
Bozeman, MT 59717-2900
pesticides@montana.edu
www.montana.edu/extension/pesticides
(406) 994-5067